183
|
CHAPTER 30
Evolution
of the Whirlwind Wheelchair
The Best wheelchair Designers? Wheelchair Riders!
Everest and Jennings is the brand name of the world's largest
wheelchair manufacturer. Many people do not realize that the original
designer and founder of this global wheelchair business was disabled and
rode a wheelchair himself. The original "E&J" wheelchair - which
was a breakthrough in its day - grew out of a disabled person's creative
response to an unmet personal need.
But as E&J Industries grew, the company became more interested in
mass-production than in innovation. Fortunately, however, other disabled
persons have continued to advance the state of the art. Like
Herbert Everest, many of the most innovative wheelchair designers in the
past 20 years have themselves been wheelchair riders. |
RALF HOTCHKISS AND THE WHIRLWIND
One of the world's most caring and creative wheelchair designers and
builders is Ralf Hotchkiss, who lives in California, USA. Ralf became
paraplegic (paralyzed from his chest down) from a motorcycle crash when he
was a teenager. Since then, Ralf trained as a mechanical engineer, and has
designed and built a wide range of innovative wheelchairs and other
equipment.
When Ralf first decided to build a 4-wheel drive wheelchair,
he had a hard time figuring a way to transfer power from the large back
wheels to the small front wheels. The obvious solution was to use bicycle
chains. But for this, the front wheels would need to not swivel (pivot) to
make turns, as do caster wheels of most wheelchairs.
Furthermore, caster wheels need to be fairly small to avoid bumping the
footrests when they pivot. But, to move easily on rough ground, Ralf's
front wheels needed to be relatively large. What to do???
The solution, Ralf explains, came from the Bible: the so-called
Ezekiel Wheel, a circle of small wheels that together form a larger wheel.
With this idea, Ralf created a front wheel made of a series of small
rubber cones, positioned in a circle around the central hub. Each cone is
mounted on its own ball bearings, so it can roll sideways, while the wheel
as a whole rolls forward. This combination of several small wheels within
a bigger one gives a multi-directional roll similar to that of a caster
wheel. However, the forward direction of the main wheel is fixed and it
does not pivot. This is what Ralf needed for his 4-wheel drive. |
184
|
Low-Cost, High-Quality Wheelchairs Made by Third World Riders
Although Ralf's 4-wheel drive wheelchair worked well, it never became
popular. Building it was too costly and time consuming. Just the front
wheels used 24 bearings and 20 individually vulcanized cones.
Ralf's interest turned to developing low-cost wheelchairs for the Third
World, using "appropriate technology." His incentive was sparked on a
visit to Nicaragua in 1980, shortly after the Sandinistas overthrew the
Somoza dictatorship. A group of young Sandinistas who had been spinal-cord
injured during the war had formed a grassroots group called
Organization of Disabled Revolutionaries (ORD). They had so much
trouble getting wheelchairs that four of their members were sharing a
single wheelchair. Most wheelchairs in Nicaragua were imported from the
USA. With the stiffening US embargo, both chairs and spare parts were very
hard to find. The ORD members had difficulty reintegrating into society
and finding work because they lacked mobility. Some, whose wheelchairs had
broken down, had gone back to dragging themselves about in their homes,
unable to leave.
For these reasons, the Disabled Revolutionaries set up a small
wheelchair repair shop. But they ran into problems. Commercial imported
chairs, such as E&Js, have poor-quality bearings which wear out
quickly in a rough, dusty environment. Because they are not a standard
size, they could only be replaced with over-priced bearings purchased from
the original manufacturer. The cost was prohibitive. In places like
Nicaragua, where bearings of any kind are often not available, wheelchair
maintenance becomes extremely difficult.
Clearly, such dependence on expensive, hard-to-maintain, imported
chairs increased people's handicaps. Ralf worked with ORD to design a
low-cost wheelchair that could be built from local materials by
modestly-skilled disabled workers. The result was the Torbellino,
or Whirlwind Wheelchair. Within a year, ORD was operating a mini-factory
in which a team of disabled persons built this home-grown design.
THE WHIRLWIND WHEELCHAIR is relatively easy
to build in a modestly-equipped shop. Yet its quality is excellent. As a
wheelchair rider himself, Ralf appreciates the need for a light-weight,
compact, easy-rolling, trouble-free chair. The design of the Whirlwind is
simple and stream-lined, but a great deal of skillful engineering has gone
into it.
The frame of the chair is made from electric-conduit steel tubing,
available in building supply stores around the world. The back wheels are
bicycle wheels. The bearings (of the early model) are standard high-speed
bearings used in small electric machinery. Used bearings can often be
obtained at very low cost in electrical repair shops. These are finely
made bearings for high speed use. Even secondhand ones, used in a
wheelchair, will long outlast commercial wheelchair bearings.
The beauty of the Whirlwind is that it is made in small
community shops by disabled people who recognize the need for a chair that
is adapted to the needs of the individual rider.
These wheelchairs tend to be custom-built or adapted. In the process, new
design opportunities arise, and the chairs come closer to matching the
varied needs of their users. |
185
|
The long-term vision:
WHEELCHAIRS FOR ALL WHO NEED THEM
Since helping ORD in Nicaragua, Ralf has traveled around the world,
facilitating workshops and helping groups of disabled persons begin to
produce appropriate wheelchairs. One of the first groups he worked with
was PROJIMO, in the mountains of Western Mexico. Over the years, Ralf has
led workshops and worked with disabled wheelchair builders in 30 countries
in Latin America, Africa, Asia, and Russia.
Ralf calculates that, of the 20 million people in the Third
World today who need wheelchairs, fewer than one percent have them.
He dreams of the day when all who need a wheelchair will have a chair
fully suited to their needs. To this end, he and his friend, Peter
Pfaelzer at San Francisco State University, formed Wheeled
Mobility, a small non-profit organization which is rapidly
turning into an international network of wheelchair builders and
designers. If there are ever to be enough wheelchairs - chairs
that are truly liberating to their riders - production must be
decentralized and the building process must be demystified, with users
leading the process.

RECENT WHIRLWIND INNOVATIONS
The basic design of the Whirlwind keeps evolving. Not
only has Ralf continued to design and test new features himself, but he
has gathered new ideas from groups of disabled persons around the world
who are building local variations of the Whirlwind.
It should be noted that many of these new features were developed in
collaboration with disabled persons who expressed difficulties with the
existing design or who wanted some particular modification.
In this book, we do not give detailed instructions for making the
Whirlwind wheelchair. A brief description can be found in the book,
Disabled Village Children. Very detailed instructions - including
suggestions for setting up and stocking a shop - are in Ralf's fine
handbook, Independence Through Mobility (see
page 343).
For years, Ralf has been revising and updating this book, but new ideas
come so fast that it is a never-ending process. In this chapter we
will give a preview of just a few of the most innovative modifications and
improvements of the Whirlwind chair. While developed primarily
for the Whirlwind, most of these innovations can be adapted to other
models, or even to commercial wheelchairs.
1. Front Wheels and Tires
The front caster wheels and tires of the Whirlwind have presented some
big design challenges. Caster wheels are complex and costly. They require
two sets of bearings, one vertical and one horizontal, so that the wheels
can swivel, as well as rotate. (The swivel is what allows the chair to
make turns.)
The basic front-caster design and the wheel forks remain much the same
as in Ralf's original book (and in Disabled Village Children). A
new design for bearings is discussed under entry #2. Here, we look at
innovations in wheels and tires.
|
186
|
FRONT WHEELS AND TIRES TO SUIT DIFFICULT TERRAIN:
A THORNY PROBLEM
Most modern commercial wheelchairs now come with tiny, hard, rubber
or plastic front wheels. These are good for gliding over hospital floors
or smooth, paved streets. But they function poorly on the rough, sandy
paths of villages, or on the pitted, irregular roads of many Third World
cities. For difficult or sandy terrain, front wheels need to be
relatively big (6 to 9 inches in diameter) and wide (1+1/2 inches or
more).
Pneumatic tires (filled with air, under pressure)
are light-weight, and on rough terrain they give a much smoother ride
(which may add to the life of the wheelchair - and the rider).
But air-filled tires also have short-comings. On rocky or thorny
paths they puncture easily and often need to be patched and pumped up.
Also, pneumatic tires that fit small caster wheels tend to be
outrageously expensive. And, in many countries, they are simply not
available. In the original version of Independence Through Mobility,
Ralf gave an address in China where pneumatic tires and tubes can be
bought in large quantities at relatively low cost. But this is hardly an
ideal solution for equipment designed to use local, easily obtained
materials.
The wheels have presented another problem. In the
early Whirlwind design, Ralf recommended making front wheels from two
discs of hard wood, glued together, with their grain crossing (at right
angles) to prevent splitting. The photos of the Whirlwind, below and on
p.195, show the wooden wheels.
These wooden wheels were tried at PROJIMO in Mexico, but many users
found them unsatisfactory. In spite of attempts to waterproof them with
heavy varnish or epoxy finish, in the mud and rain they soon rotted and
cracked. Riders in other countries reported similar problems. Another
problem was that some people who wanted to purchase a wheelchair thought
wooden wheels were primitive and ugly. They insisted on having "modern"
wheels, even if more costly. Whatever the reasons, such preferences must
be taken into account.
Molded aluminum wheels were another alternative
considered by Ralf.
Workshops in Brazil and Bangladesh cast and lathe-turn their own
aluminum wheels. But for most small production centers, this is
impractical. The set-up costs are prohibitive. |
187
|
A rubber T tire, clamped between metal plates. A
new design came from RESCU, a production center in Zimbabwe where
disabled workers build assistive equipment, including the Whirlwind
wheelchair. The front wheels consist of two round sheet-metal
plates which grip a molded rubber tire.
The tire, in cross section, is T-shaped. The center-arm of the T
projects inward, and is firmly held with bolts between the 2 metal
plates. The tire is vulcanized (heat-molded) in a specially
lathe-turned steel mold. Once the mold is made, any shop that retreads
car tires can produce these T-tires in small or large quantities at a
relatively low cost.
The wheel is made by cutting two round disks of sheet metal. The
disks must be widely separated at the center to hold the hub firmly,
and shaped so they can grip the T-tire. A dye of lathe-turned steel is
needed to hammer, press or spin the disks into shape.
The advantage of this Zimbabwe wheel is that, after a (fairly
costly) initial investment for the molds and dyes, the production cost
can be quite low. The tire, made of the same rubber as a car tire, is
nearly indestructible. Its broad, T-shaped base has almost the same
flexibility and springiness as a pneumatic tire. But it never
punctures. Wider tires can be made for sand, to prevent sinking in.
Problem: In Zimbabwe, the wheel was made
of fairly thick sheet metal, pressed into shape in a large metal-press
delivering tons of weight. In redesigning the wheel for smaller shops
without such massive presses, Ralf began to experiment with a thinner
grade of sheet-metal that could be hammered into shape when the metal
disk was clamped over a dye. The PROJIMO wheel-chair builders tried
making these wheels. At first, they appeared to work well. But, after
repeated bumps into rocks and curbs, the metal disks bent and finally
collapsed. The PROJIMO team tried using thicker sheet-metal, but it
was too difficult to hammer into shape. Groups experimenting in other
countries ran into similar problems.
Solution: An all-rubber wheel and tire.
After exploring many possibilities, Ralf found a simple solution.
Do away with the sheet-metal disks and mold the entire tire
and wheel out of vulcanized rubber, as a single unit.
The central part of the wheel is cast thick enough to make it
inflexible. The wide outer-edge that rolls against the ground is thin
enough to provide a spongy flexibility.
The wide center-part of the wheel is molded to grip the hub. A
flange, welded to the hub, is bolted to the wheel.
A big advantage to this all-rubber wheel is that it bends easily,
to ride smoothly over irregular terrain. These simplified wheels show
great promise. Eventually, they may be used for both front and rear
wheels ofall-terrain wheelchairs. |
188
|
2. Bearings
Among the biggest problems with many wheelchairs are the bearings.
Commercial chairs use off-size ball bearings of relatively poor
quality. They soon wear out, making the wheels wobbly and hard to
push. Since the bearings are not a common size, often they cannot be
replaced locally, but must be obtained at high cost from the
wheelchair supplier or the manufacturer. Where chairs are imported,
this may be very difficult or impossible. The Third World is littered
with carcasses of fancy imported chairs whose bearings wore out.
For this reason, the original Whirlwind design
uses local, widely available bearings. If dust or dirt get into
the bearings, it can ruin them. So, sealed bearings are
recommended. Though more costly, the user saves money in the long
run.
Second-hand high-speed, sealed bearings of a workable
size (5/8 inch inside diameter, 1+3/8 inch outside diameter - or
15 x 35 mm metric equivalent) can often be found in junk yards (in
starter motors of old cars) or in small motor or power tool repair
shops. (For more details, see Independence Through Mobility.)
Problem: When PROJIMO began making wheelchairs, it
could get all the second-hand bearings it needed free or at low
cost from friendly repair shop owners in the closest cities. But
as the program produced more and more chairs, the repair shops ran
out of second-hand bearings. PROJIMO had to buy new bearings,
which were very expensive. The 12 sets of bearings needed for a
wheelchair cost as much as all the remaining materials! This
pushed up the price so much that many poor families could not
afford it. Many other wheelchair-making shops have had a similar
experience. |
|
Solution: An idea to solve this problem
came from India. On a visit there, Ralf Hotchkiss inspected the huge
wheels of the traditional ox carts. They used an ancient form of
rod bearing, or "needle bearings." The wheels rolled
on a series of metal rods which fit snugly between the iron hub and
the axle.
Ralf experimented with hubs that, instead of ball bearings, use
metal rods that roll between the axle and the hub tube. But the rods
sometimes jammed in the hub.
An
old mountain farmer in the eastern USA solved this problem by showing
Ralf that thinner rods in a longer hub do not jam. Ralf now uses
carpenter's nails with their heads cut off. The nails form a circle of
rollers between the axle bolt and metal hub tube.
Ralf has tested the ease with which the wheels turn compared to
ball bearings, and finds them equal. The cost of materials for rod
bearings is a fraction of that of commercial ball bearings. Rod
bearings require more work, but durability tests indicate that they
last many times longer. (Whereas ball bearings bear the weight of
chair and rider on a tiny point on each tiny ball, with rods, the
weight - and wear - is spread over the full length of the rods.)
These new (though ancient) bearings show great promise. Hopefully
they will contribute toward providing high-quality, long-lasting
wheelchairs to many of the millions of people who need them, at a cost
more within their reach. |
189
|
3. Folding Mechanism, with Adjustable Chair Width
Different adjustments on wheelchairs. People who
ride wheelchairs come in all shapes and sizes. So should wheelchairs.
Many commercial chairs - although the basic models are standardized -
come with adjustable footrests, armrests, and alternative positions
for the rear hubs.
Hub position. By changing the up-and-down position
of the hubs in relation to the chair, the height and tilt of the seat
can be changed. By changing the front-to-back position of the hubs,
the balance of the chair can be changed. For example, a person without
legs may need the rear hubs mounted farther back to avoid falling over
backwards when going up-hill.
An advantage to producing wheelchairs in small,
community-based shops is that often they can be custom-made.
Rather than adding a lot of mechanisms for adjustments to meet
different user's needs (which add to both weight and cost), each chair
can be personalized from the start, to meet the specific needs of the
intended user. If the wheelchair makers are also wheelchair riders,
they are likely to be more aware of and responsive to those needs, and
to include the user in the planning and design process.
Nevertheless, even in a small community shop, some amount of
standardization can make production quicker, easier, and cheaper. It
helps to have a selection of ready-made chairs available when they are
needed. That way the person can try different chairs and pick the one
that comes closest to meeting her or his needs. Last minute
adjustments (or even more substantial changes) can then be made
according to the individual's requirements.
Goodness of fit - in terms of size, width, seat angle, angle and
height of back, need for armrests, position of footrests, etc. - is
essential. Decisions need to be made with the user, not
for her, allowing enough time to test different alternatives and
make well-informed decisions.
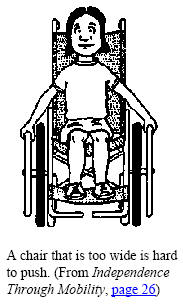
ADJUSTABLE FEATURES OF THE WHIRLWIND.
Although the Whirlwind has a basic (if evolving) design, it can be
built and modified in different ways for different users. The
height of the footrests can be easily adjusted by the user.
Also, in response to his own need and that of others with spastic
ankles, a PROJIMO wheelchair builder, Martín Pérez (see Chapters
37 and 39),
has designed a simple way to adjust the sideways angle of the
footrests.
One of the greatest needs for adjustability in wheelchairs is the
width of the seat, and thereby the width of
the whole chair. Correct width is important for the stability
and comfort of the rider, and for her ease in pushing the chair. A new
design for easy adjustment of chair width has been developed, together
with a new mechanism for folding the chair.
|
190
|
Folding is important.
For many wheelchair riders, it is essential that their chair can fold,
to fit into a narrow space. This is especially important for those who
need to travel in a bus, carry their chair in the back of a car, or
pack it on a donkey.
Problem: The original Whirlwind design
included an upright X-brace that folded like scissors, as do most
commercial chairs. But to fold well, the measurements, welds, and
alignment must be exact. In PROJIMO, as in many small shops run by
disabled persons, many workers are still learning their skills. There
are few highly skilled crafts-persons. The resulting wheelchairs were
often very difficult to fold. Users expressed their frustration.
Solution:a horizontal folding device. To
solve this common problem, Ralf and friends experimented with
alternative folding devices until they came up with one that was more
fool-proof. The new design folds horizontally, rather than vertically.
Although it has more pieces and uses more welds than the X-brace, it
requires less skill and precision to build, and gives consistently
good results. PROJIMO now uses this new folding device in all its
Whirlwind chairs, and has had fewer complaints.
Narrowing the chair to get through doorways. On
experimenting with the new folding mechanism, users discovered that
they could easily narrow the width of the chair while sitting in it.
They pull the handle under the seat forward, and then pull the wheels
in, closer to their body. This offered a solution to another big
problem of wheelchair riders in many countries: getting through narrow
doorways. (See Luz's story on page 17.)
With the new design, to go through a narrow door the user simply
pulls the sides of the chair in against her hips, and rolls through.
(With an X-brace, narrowing the chair is much harder, because it folds
against gravity and the person's own weight holds it wide open.)
Adjustable chair and seat width. The horizontal
folding mechanism also lends itself to adjusting the seat width to
match the hip-width of the user. Small holes can be drilled in the
cross bars of the adjustment device, so that the chair width can be
adjusted, depending on which set of holes the center bolt is passed
through. |
191
|
Upholstery. To avoid
having to make new upholstery with different measurements for
different seat adjustments, Ralf has devised wrap-around seat and
back-rest cloths that can be laced up at different widths.
The patterns for the back-rest and seat are similar.
They consists of one square just a little bigger than the desired size
of the back-rest or seat, and another square, 4 times as big.
Hem the edges of both squares to prevent fraying. Then, fold the
big square in half, and cut grooves as shown here. Sew together at all
edges, except where the small square will be attached. Turn the
resulting sack inside out, and sew on the small square. Make holes for
lacing as shown.
How appropriate is the new folding mechanism and adjustable
seat?
The answer depends on who you ask. Wheelchair riders and users
(including Ralf) have mixed feelings. One of the beauties of the early
Whirlwind design (with the vertical X-frame) is its simplicity,
streamlined look, relatively few parts, and few welded joints (all of
which contributed to the chair's low weight and low cost).
The new folding mechanism with its adjustable seat width solves a
number of problems but sacrifices some of the Whirlwind's graceful
look and adds a bit of weight. Some users like being able to adjust
the chair to their own body width, and to narrow it easily to pass
through narrow doorways. Other users think it "looks funny" and prefer
the more conventional X-brace. (For some people, appearance is more
important than function.)
The PROJIMO wheelchair builders are delighted because - although
the new folding mechanism takes more welds and looks more complex -
for them, it is easier to build successfully. That is important.
Designs must be appropriate for builders as well as users.
The search for better designs continues. Ralf's team is now
experimenting with a folding mechanism developed by blacksmiths in
Nyabondo, Kenya. This uses a vertical X-brace that is easier to build
than is Ralf's original design.
There is always room for improvement.
And improvements are always possible when builders and users work
together creatively. |
|